Summary:Carbon fiber tube has the performance advantages of light weight and high strength. It can play a good weight reduction effect in actual production and application, and can well achieve the effect of reducing energy consumption. Carbon fiber tube can......
Carbon fiber tube has the performance advantages of light weight and high strength. It can play a good weight reduction effect in actual production and application, and can well achieve the effect of reducing energy consumption. Carbon fiber tube can be used as a substitute for many product accessories, such as Carbon fiber drone arms, carbon fiber robotic arms, carbon fiber rollers. Then this article will talk about how to improve the performance advantages of carbon fiber tubes.
The common production processes of carbon fiber tubes include roll forming, winding forming, compression forming, pultrusion forming, etc. Different specifications and shapes of carbon fiber tubes require different production processes. For example, carbon fiber square tubes and rectangular tubes are molded by molding, and carbon fiber round tubes are rolled and wound. The product performance of carbon fiber tubes has a lot to do with the production process. The production costs of carbon fiber tubes under different production processes are also different. Here we will improve the performance of carbon fiber tubes according to the process points.
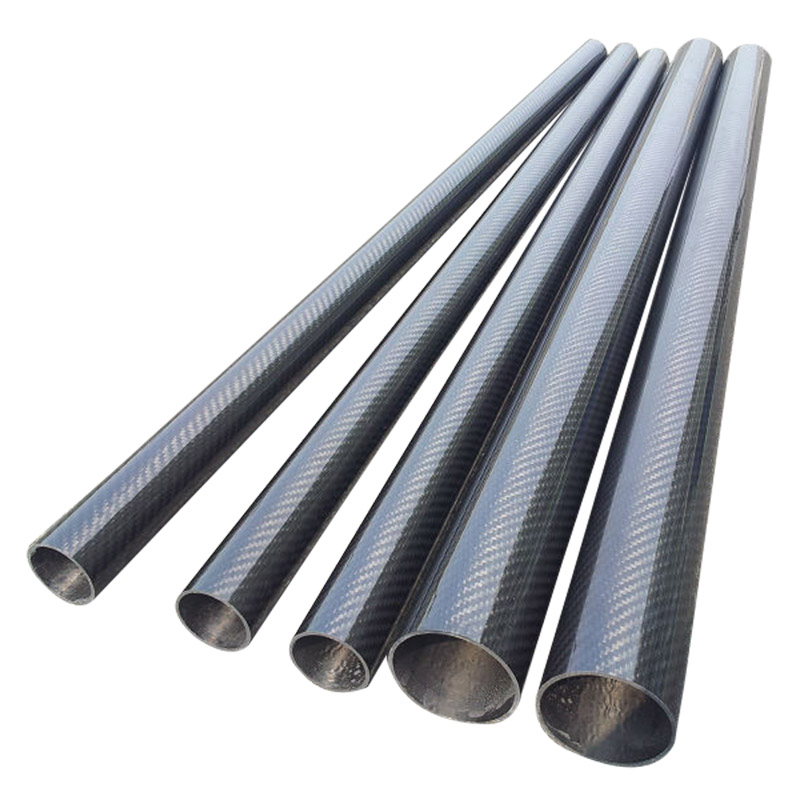
In the production process of carbon fiber tubes, attention should be paid to control each step, otherwise there will be faults, splits, wrinkles, bulges, etc. The high probability of these situations occurs because the carbon fiber prepreg is not pressed when laying up. As a result, the prepreg layers are relatively loose in the early stage, and during the hot pressing process, the resin in the prepreg will gather in a certain place to form a block, or there is air between the layers, which will cause the prepreg to clump together. These will cause the carbon fiber prepreg to be delaminated and the mechanical properties of the product will decrease. It is necessary to pay attention not to loosen the layers when laying up the layers. When laying up products with thicker walls, it is necessary to lay several layers and then do it once. compaction treatment. In the case of compression molding and autoclave molding, the airbag vacuum can be used to compact the prepreg more tightly and improve the mechanical properties of the carbon fiber tube.
carbon fiber helmet factory
The molding of carbon fiber tubes needs to be made with the help of molds, so there are high requirements for the dimensional accuracy of the molds. In general, the production of carbon fiber tubes does not require high quality and inner diameter, but the requirements for outer diameter are very high, which requires controlling the accuracy of outer diameter. If a hard aluminum core mold is used, it can be produced by the thermal expansion of hard aluminum Cure internal pressure to increase its density and mechanical properties.
In the actual production process, due to the different production technology and experience technology mastered by each enterprise, the quality of the produced carbon fiber tubes is also different.
Founded in 2006, Jiaxing Longshine Carbon Fiber Products Co., Ltd. is China Custom Carbon Fiber Composite Manufacturers and OEM Carbon Fiber Material Suppliers, located in the center of Yangtze River Delta, the state-level Xiuzhou High-tech Industrial Development Zone of Jiaxing. In recent years, we committed to the r&d and production of carbon fiber and other composite materials in the military and civil fields, including participating in the R&D and production of C919 aircraft parts, high-speed rail accessories, and several logistics support projects.